

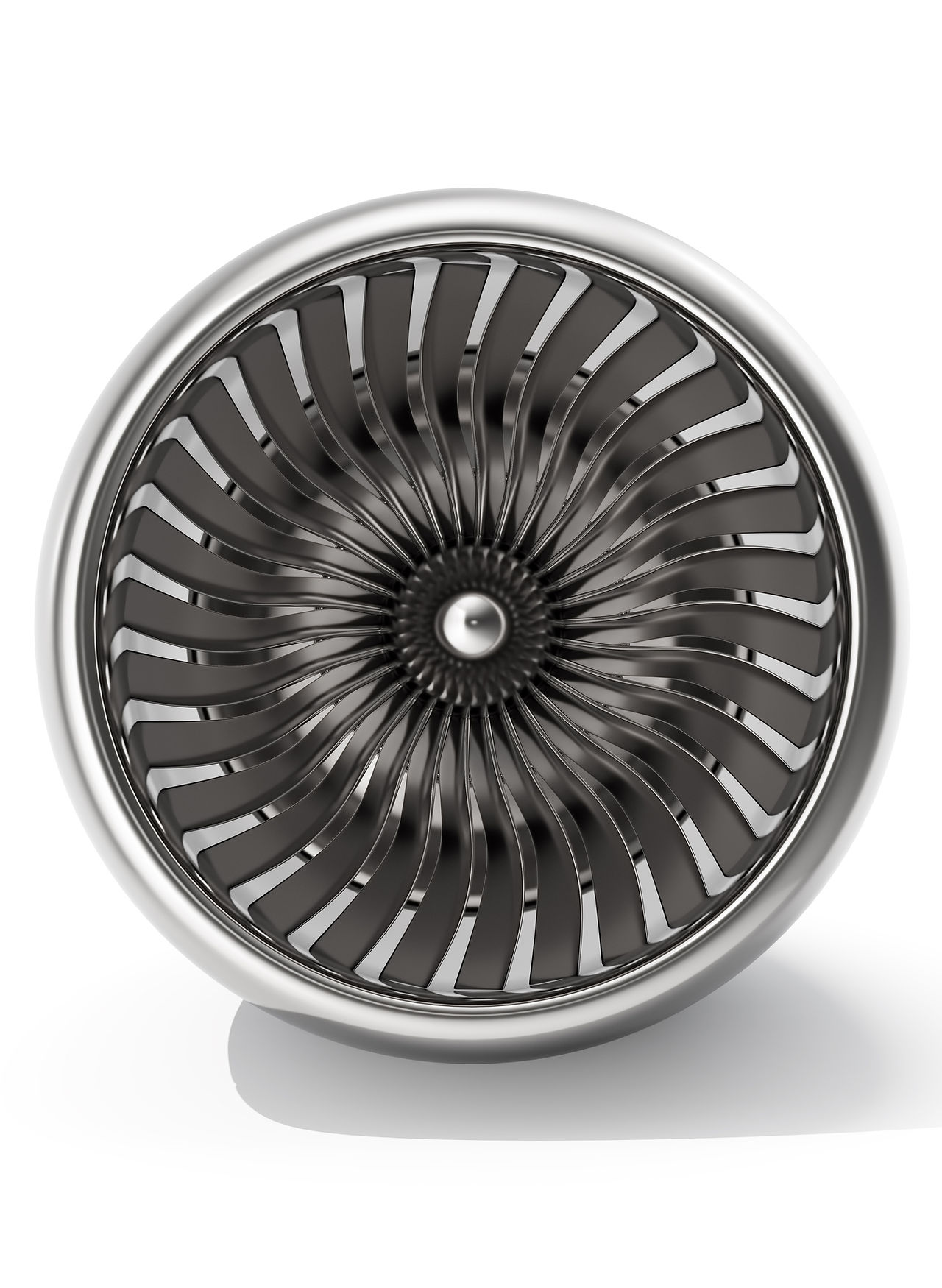
>
>
>
Fuel Accessory Test Facilities
Fuel Accessory Test Facilities
Our brushed stainless-steel range of Universal Fuel Accessory Test Facilities, provide and ideal acoustically treated Fuel Control Unit Dual Direction Thyristor Drive Systems up to 15,000 RPM and 25-130 kW (33.5 - 174HP). They include altitude P2 sensor environments of 15,240 Metres (50,000 ft) and minus 65 centigrade (-85F). Systems contain their own stainless steel reservoir tanks with integral de-aeration, level indication, 5-micron filtration and pump/pipe sizing capacities optimised to suit the customers flow/pressure requirements.
In today’s environment most of our fuel test benches are fully computer controlled and provide complete measurement and test results recording. Our software can even prompt the operator through each OEM test instruction. Are fuel test facilities can run on Avtur (Jet A1) or Aviation Calibrating Fluid Type II, they are also available with fully integrated cooling systems and fully enclosed, ventilated and illuminated Fuel Nozzle Patternization Cabinets.
Each facility is pre-commissioned prior to delivery on a “Turnkey” basis, to fully support the repair and overhaul of aero engine related accessory components. Our multi component test facilities are designed for a wide range of flows, pressures and drive speeds. A high-speed real-time data acquisition system provides production versatility and improved quality of test recording.
-
A Multi-purpose Universal, Pre-commissioned Fuel Accessory Test Facility includes the following:-
-
Ergonomically designed brushed stainless steel panels for durability, eliminating FOD risks associated with painted surfaces.
-
Self-sealing, stainless steel panel couplings for fast adaptability and cleanliness.
-
A multi-adaptable component drive head, with variable speeds up to 15,000 RPM, providing true long term flexibility.
-
Digital controls for the DC Thyristor drive speed, for perfect speed stability irrespective of load.
-
Aerotest’s optional, well proven high speed data acquisition systems and PC-Based component test software.
-
Integral mains power distribution panel, with low voltage 24 Volt D.C contactor control for personnel safety.
-
Cabinet lighting both front and rear for test component adjustment and plant maintenance.
-
Optional integral slave oil system for FCU Spline lubrication configurations.
-
End to end calibrations, over 20 points prior to commissioning and cross correlation, using our NAMAS traceable instrument calibration equipment.
-
The pre-proven test systems are available with and without fuel burner patternization cabinets, preformed base frames and altitude temperature simulation.
-
Electricity, fuel/calibrating fluid and cooling water connections are all that is required by the customer, following installation, to achieve instant production capability.